How it works
Rubber and plastic parts are placed in a stainless steel parts basket,
which rotates in a blast chamber evenly exposing all parts to
the blast media. The chamber is insulated with rigid polyurethane
foam to ensure stable temperatures.
Liquid nitrogen lowers the interior
temperature, freezing the flashing to make it brittle. Use of
high-purity, moisture-free nitrogen eliminated the need for a dryer
and prevents part contamination due to moisture.
The high-speed impeller shoots polycarbonate plastic pellets into
the chamber. Traveling at high speeds, these pellets cleanly trim
off the inner and outer diameter flashing of parts in one operation.
The unit is fully enclosed to
minimize ambient noise levels. Blast media and flash can be separated
and recovered for reuse.
- Benefits of
This Unique Process
Greater Productivity
Cryogenic deflashing trims parts
in seconds. This is much faster than chemical stripping, molten
salt baths, incineration, rotary tumbling, and hand sanding. As
a result, more parts can be deflashed in less time.
Better Product Quality
The high temperature of molten
salt baths and incineration can distort parts. Cryogenic deflashing
keeps parts cold to preserve their integrity. Use of plastic
blast media prevents the scratching caused by hand sanding and blasting
with abrasives such as sand, steel shot, aluminum oxide, or glass beads.
Environmentally Sound
The nitrogen cryogen can be
recycled or vented safely to the atmosphere. The use of toxic chemicals
and the problems associated with their disposal are completely
eliminated. In addition, cryogenic deflashing systems are typically
enclosed to minimize noise.
Improved Plant Safety
Cryogenic deflashing prevents
the splashing that can occur when using a molten bath. It also
gets rid of toxic chemical fumes and dust associated with chemical
stripping and manual deflashing.
Simple Operation
Highly automated, today's
cryogenic deflashing equipment is easy to use. Cryogenic systems can
be configured to deflash rubber, plastic and metal products in a
wide range of materials, sizes, and shapes. Compact design permits
installation even when space is limited.
Custom Deflashing
We do offer custom deflashing.
We charge by the per load basis. A load (amount of parts) will
be established once we receive your parts. We can also estimate the
amount of parts, if you fax us a drawing/sketch prior to sending in
the parts.
Sample Deflashing
Tests
We invite you to send us
some of your parts for sample deflashing tests. This will enable you
to review the quality of deflashing our equipment can achieve. In order
for us to establish parameters for the parts you send, please identify
each, by your part number, the main compound used in the manufacturing,
along with a finished or Q.C. example. We use this as a guide to your
expected quality level.
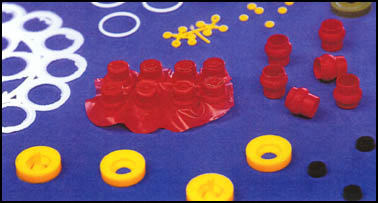
|